Choosing the right pallet racking system for your warehouse can feel overwhelming, but making the right decision can transform your operations, save space, and improve safety. Whether you’re setting up a new warehouse or looking to upgrade, this guide will walk you through everything you need to know to make the best choice for your specific needs.
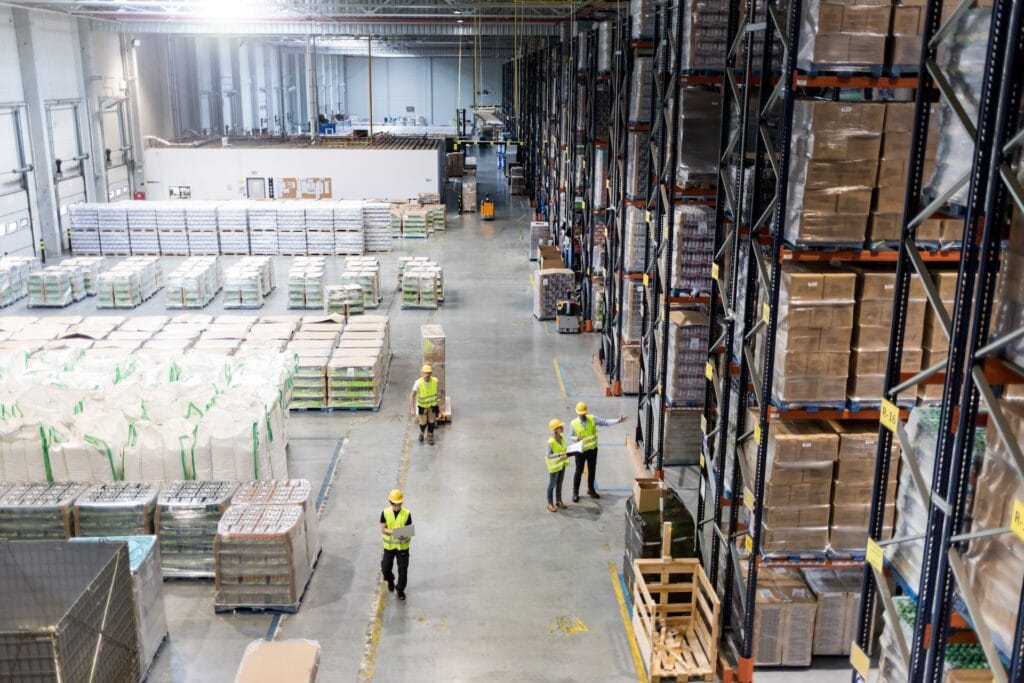
Why Your Choice of Pallet Racking Matters
Pallet racking is more than just storage; it’s an investment in your warehouse’s efficiency and future growth. The right racking system can help you:
- Maximise space: Get the most out of your warehouse’s square footage by going vertical.
- Increase efficiency: Streamline product retrieval and inventory management.
- Ensure safety: Reduce accidents by choosing a system that fits your load requirements and workflow.
Whether you’re dealing with high inventory turnover or large, bulky items, there’s a solution for you. But before jumping in, it’s essential to evaluate your unique needs.
Assessing Your Warehouse Needs
1. Available Space
Start by measuring your warehouse’s dimensions, including floor space, ceiling height, and access points like doors and loading docks. This will help you determine the maximum height your racking can go and how much floor space it can occupy without interfering with traffic flow.
- Pro tip: Think about expansion. If your business is growing, leaving space for additional racking or extensions is a smart move.
2. Product Characteristics
The size, weight, and quantity of the products you store play a huge role in your choice. Ask yourself:
- Are your products uniform in size, or will you need to store different shapes and weights?
- Do you require direct access to each pallet, or are you okay with a “first in, last out” system?
3. Turnover Rate
How quickly do you need access to your products? Fast-moving goods require racking systems that allow for quick and easy access while slower-moving products can be stored in more space-efficient ways.
Types of Pallet Racking Systems
Now that you’ve considered your needs, let’s explore the most common types of pallet racking systems available. Each has its pros and cons, so it’s crucial to match the system with your operational demands.
1. Selective Pallet Racking
Selective pallet racking is the most common type and offers direct access to each pallet. This system is ideal if you need to retrieve products frequently and individually.
Benefits:
- Easy access: Perfect for warehouses with high inventory turnover.
- Customisable: Adjustable beams allow for flexibility in rack height and pallet size.
Best for: Warehouses with a wide variety of products and fast-moving inventory.
2. Drive-In/Drive-Through Racking
Drive-in or drive-through racking is perfect for high-density storage where you don’t need access to every pallet at all times. In a drive-in system, forklifts enter the racks from one side to pick up or place pallets. Drive-through systems allow access from both ends.
Benefits:
- Maximises space: Allows for more pallets per square foot compared to selective racking.
- Cost-effective: Ideal for storing large volumes of identical items.
Best for: Warehouses that deal with bulk storage and have lower turnover rates.
3. Push-Back Racking
Push-back racking allows pallets to be stored on inclined rails. When one pallet is removed, the one behind it moves forward, meaning you have access to multiple pallets but only need one loading aisle.
Benefits:
- High-density storage: Stores multiple pallets deep.
- Time-saving: Reduces the need for multiple aisles.
Best for: Warehouses with a medium turnover rate and a mix of storage density and access needs.
4. Cantilever Racking
Cantilever racking is designed for items that are long or bulky, such as timber, pipes, or steel bars. It consists of vertical columns with arms extending out to support the load.
Benefits:
- Flexible storage: Perfect for non-palletised items.
- Adaptable: Can be customised for various lengths and sizes of products.
Best for: Warehouses dealing with long or awkwardly shaped materials.
How to Choose the Best Pallet Racking for Your Warehouse
Now that you know the different types of racking, how do you make the final choice? Here’s a step-by-step guide.
1. Consider Your Budget
Your budget will heavily influence which system you choose. Selective racking is usually the most affordable, but it might not be the best option if you need high-density storage. Drive-in systems are cost-effective for storing bulk goods but come with a trade-off in accessibility.
- Pro tip: Don’t just think about the upfront cost; consider long-term savings in space utilisation and productivity.
2. Think About Future Expansion
Even if your warehouse meets your current needs, think about where your business is headed. Will you need more storage in the future? Choose a system that can grow with you. Adjustable and modular systems can save you money in the long run.
3. Ease of Access and Product Flow
Consider how easy it is for your team to access the products they need. If speed is a priority, selective racking may be the way to go. However, if you’re more concerned about space and less about access speed, a drive-in or push-back system might be better.
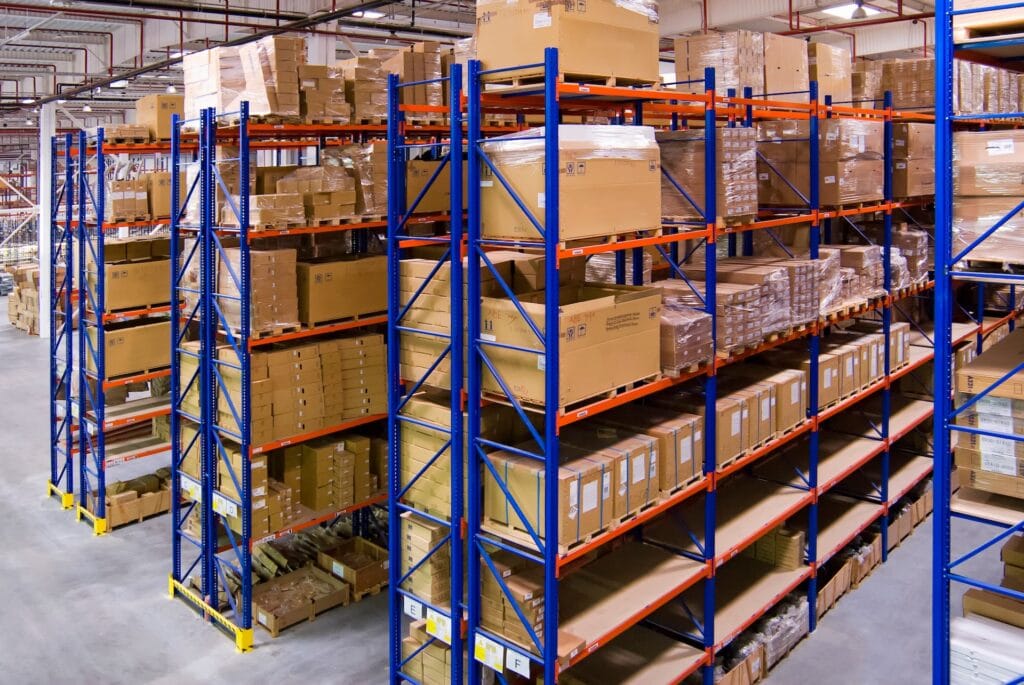
Maximising Space Efficiency with Additional Solutions
Racking isn’t the only way to maximise space. Here are a few other solutions that can complement your pallet racking system:
1. Mezzanine Floors
Installing a mezzanine floor can double or triple the usable space in your warehouse. These structures create an additional level above your existing floor, perfect for extra storage or office space.
- Pro tip: Mezzanines are perfect for expanding storage without moving to a new location.
2. Vertical Storage Solutions
If you’re short on floor space but have plenty of vertical clearance, consider high-density vertical storage solutions, such as automated systems that make use of the full height of your warehouse.
Safety Considerations
Safety should be a top priority when installing any pallet racking system. Here are a few things to keep in mind:
1. Weight Load Capacity
Make sure your racking system can handle the weight of your products. Overloading can lead to rack failure and accidents. Check the manufacturer’s specifications and adhere strictly to load limits.
2. Regular Inspections
Pallet racking systems should be inspected regularly to ensure there are no signs of wear and tear, such as rusting or bending. Damaged racks should be repaired or replaced immediately to prevent accidents.
3. Use Protective Measures
Install safety features such as rack guards, column protectors, and end-of-aisle barriers. These add an extra layer of protection for both your products and your workers.
Working with a Professional to Install Your Racking
While some businesses may attempt to install pallet racking themselves, it’s usually a better idea to work with professionals. A certified installer will ensure that your system is set up correctly, adhering to safety standards and maximising space efficiently.
What to Look for in a Supplier:
- Experience and expertise: Choose a company with a track record of successful installations in your industry.
- Customisation options: Ensure the supplier can customise the racking system to fit your specific needs.
- After-sales service: A good supplier will offer maintenance services and be available for future support if issues arise.
Conclusion: Investing in the Future of Your Warehouse
Choosing the right pallet racking system for your warehouse is an investment in your business’s future. It’s not just about storage; it’s about creating an efficient, safe, and scalable environment where your operations can thrive. By carefully considering your needs and understanding the options available, you can select a system that will grow with your business, improve workflow, and keep your team safe.
Remember, it’s always worth consulting with a professional to ensure that your pallet racking system is the perfect fit for your warehouse. With the right planning, your investment will pay off for years to come.